Toronto architect Tye Farrow has developed an ICU design with a striking, fast-assembly innovation at its core.
Under the strain of a quick-moving pandemic, our healthcare systems have never been more scrutinized, down to the very details of how care is delivered: EMT professionals, doctors and nurses are finally seen as heroic, the dearth of PPE supplies are a global concern, the underfunding of seniors’ facilities a moral and ethical scandal. We need to address the very infrastructures holding up our social safety nets – but what about the spaces themselves? How are hospitals, and particularly the way they are designed, contributing to healing, or not, in this time? How can rapidly deployable, modular hospitals present some clues as to how we can build better healing spaces from here on out? From Mass Design Group to Carlo Ratti Associati, new guidelines and models have been proposed. And now, Toronto architect Tye Farrow has also come up with an ICU concept that could influence how we design these spaces for salutogenic results.
“The under-riding value is how can environments cause health,” Farrow says. The architect has designed numerous medical facilities around the world that integrate biophilic design; one of his firm‘s most notable projects is the Credit Valley Hospital in Mississauga, Ontario, where Douglas fir glulam beams take on the appearance of trees soaring through the atrium. He has spent decades rethinking what the hospital experience could be and how better-designed spaces can mentally and emotionally supercharge us, an expertise he has recently honed with a Master of Neuroscience applied to Architecture and Design at the University of Venice.

His Solace Rapid Assembly – High Performance Covid-19 Inpatient Bed Solutions system is designed to battle staff burnout and to elevate patients’ moods and capacity for healing; it proposes a “faster, cheaper, smarter, safer” response to “some of the temporary hospital solutions we have seen built to date globally.” Farrow cites the shipping containers being used in Italy – “it’s a good solution, but it’s not good for medical staff” who need more space to work around the patient – and the tent hospitals going up in convention centres, with no access to natural light, in New York and Calgary. “Maybe they’re great for the short-term, but history has shown us there’s the first wave… and the second wave is worse.”
At the core of his ICU unit design is a 12-bed ward measuring 15 by 30 metres. The patient rooms, where party walls feature small windows for nurses to keep an eye on adjacent units, wrap around three walls; at the centre is a medical team zone and along the fourth wall are the staff support areas. At the centre, the ceiling is lifted to create a lantern volume lined with a four-sided clerestory window. “In this way, we could give the light and the change of day to the staff, which is really important,” says Farrow. For patients, being able to perceive shifting light conditions – “a passing cloud, a sudden rainstorm, the warm colour of afternoon light, gentle moonlight or the early-morning rising sun” – is also beneficial. Just as medical staff are enriching the oxygen for COVID-19 patients, this type of design that responds to circadian rhythms would also enrich the environment itself and help alleviate some of the stress felt by medical staff working in the most pressurized conditions imaginable.
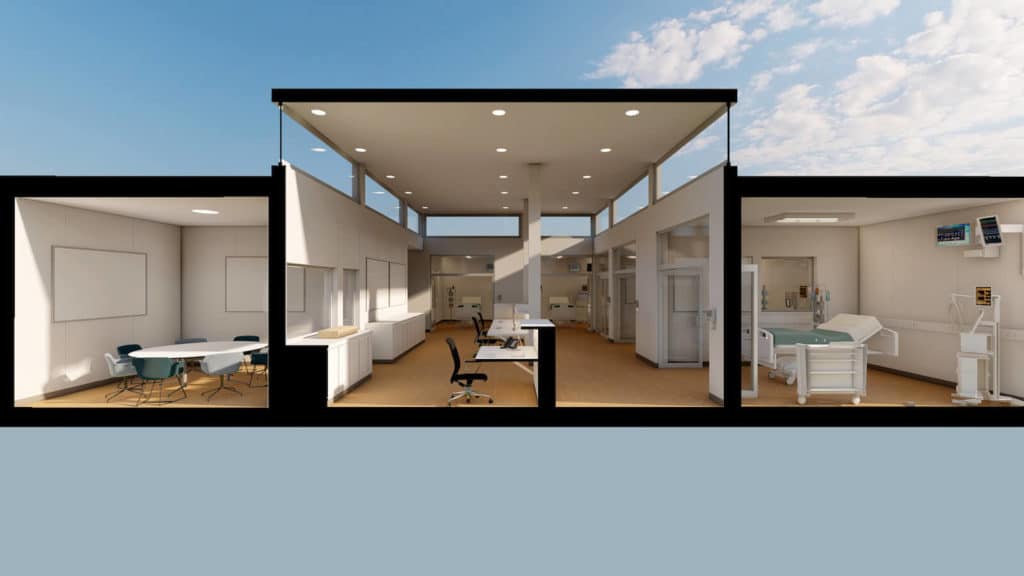
The basic building block of this 12-bed ICU ward – which can be multiplied for units of 24 beds, 36 beds, 48 beds and upwards – is just as innovative: Farrow has helped to develop the Grip Timber Cross Laminated Block (GTCLB). It is made up of layers of cross-laminated timber (the wood offcuts of shipping skids) which are adhered together with very thin strips of a “metal velcro” – an innovation of a glue-free brake pad created by the Canadian company Nucap – and stamp-pressed into modules. Grip metal bonds easily to a variety of sheet materials, from plastic to wood, and in the case of the bricks, also allows them to hook onto each other to create a “massively strong solution,” Farrow says, “It’s the equivalent of a concrete block in section and size, but lighter – which doesn’t exist in the world right now.” A single press can make 1,000 in an hour, and they can be stacked, into walls or furniture, without the use of skilled labour. Farrow likens them to Lego for their ability to be quickly assembled and disassembled.
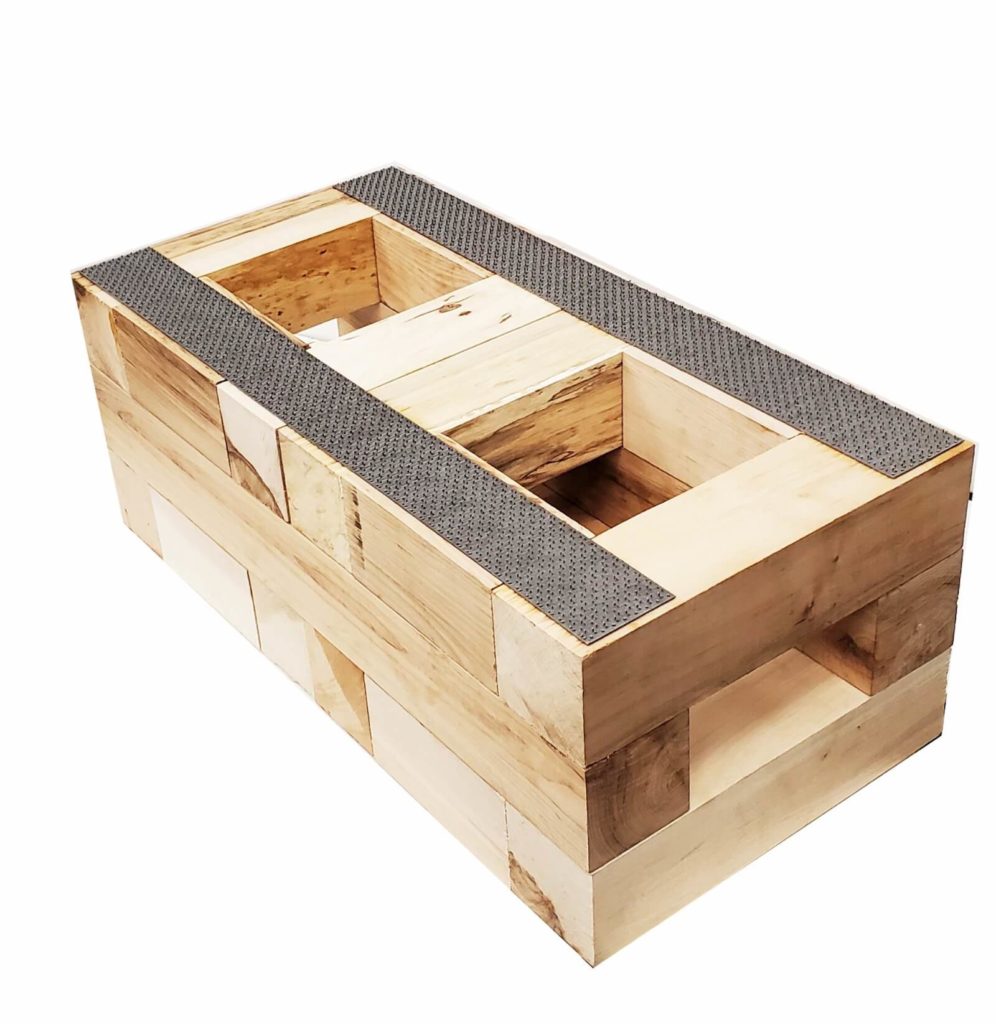
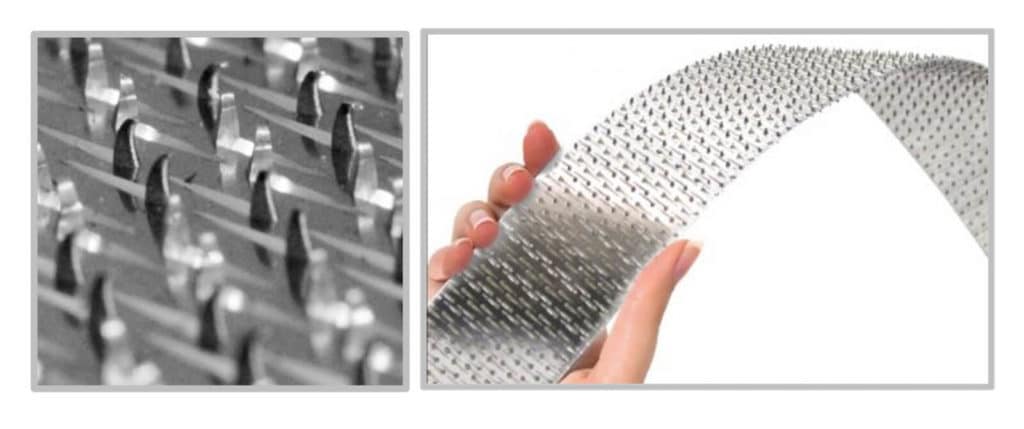
Once they are stacked, a vertical tie rod secures them together from the top to the bottom of the wall. The 25-centimetre-long blocks also have internal cavities, like a typical concrete block, allowing any mechanical or electrical conduits to be run through them. In the ICU unit, the walls would be made of this block and covered in fibre-reinforced panels that meet healthcare-setting requirements – though he notes that the wooden blocks look great unfinished – and the floor would be covered in a grip-metal flooring system that can integrate heating systems and withstand heavy foot traffic.
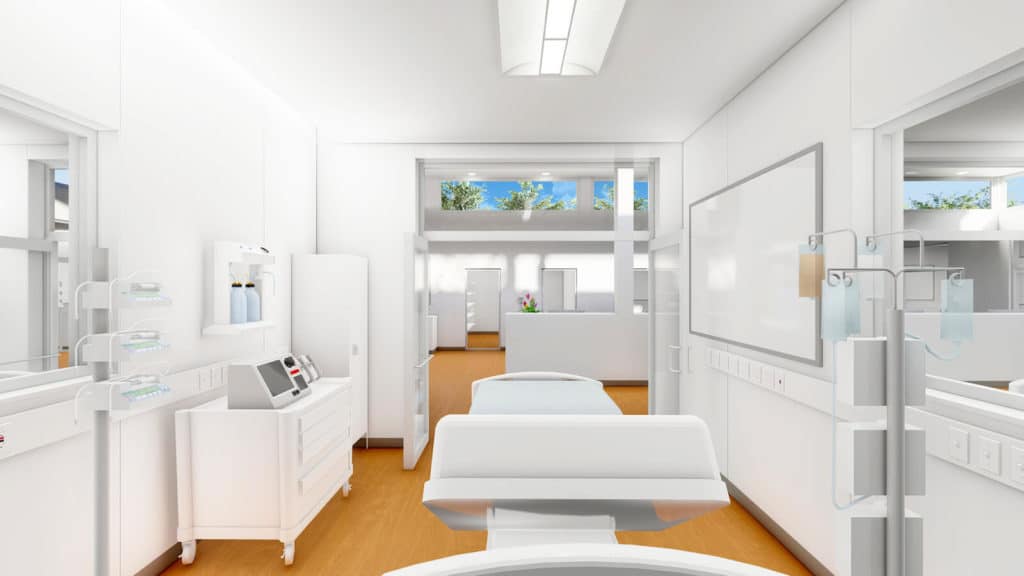
At the moment, Farrow is in discussions with health authorities in Israel, the U.S. and Canada, and applying the block innovation to other potential uses. “Interestingly the uptake isn’t only for the ICUs,” he says, “but in also helping solve some of the long-term-care home challenges.” The building block technology could also help provide affordable housing both in the city and in northern communities. “Northern First Nations communities that have a sawmill can now produce their own block, by simply buying the grip strips and having a press, and their communities can build their own homes.” He cites other ways that the block can help in rapidly deployable architecture: for instance, laneway houses that could be accessory dwelling units for elderly parents or children moving back home.
“Over the last two week we have perfected the block; it is really, really amazing,” says Farrow. “Dimensionally perfect, so functional to assemble. . . and beautiful.”